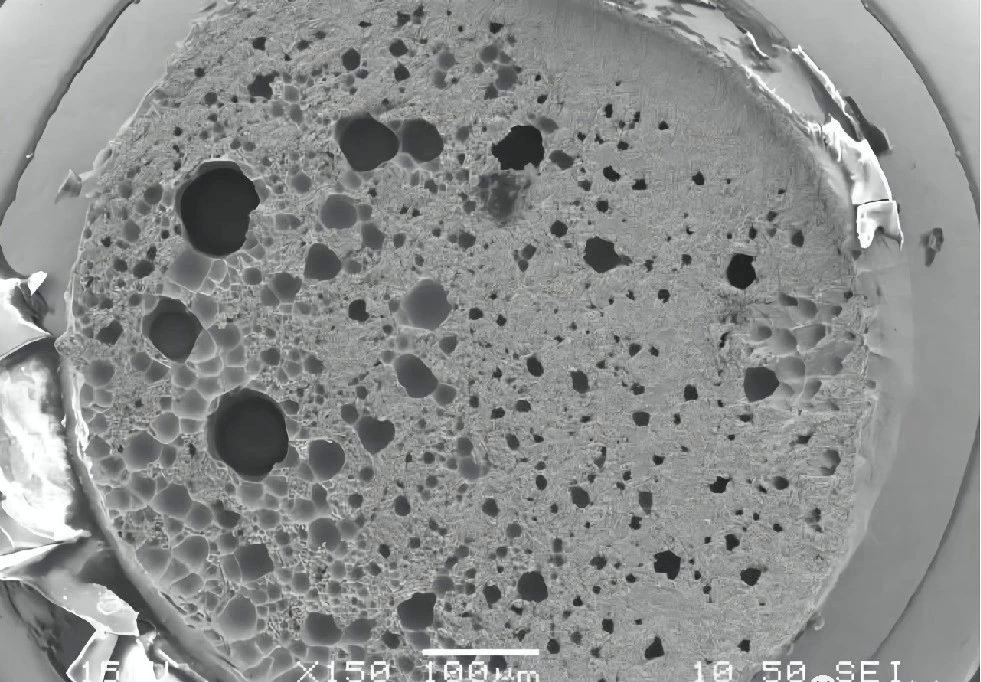
1 Pengenalan
Dalam pemasangan papan litar, tampal pateri dicetak pada pad pateri papan litar dahulu, dan kemudian pelbagai komponen elektronik dilekatkan. Akhirnya, selepas relau aliran semula, manik timah dalam pes pateri dicairkan dan semua jenis komponen elektronik dan pad pateri papan litar dikimpal bersama untuk merealisasikan pemasangan submodul elektrik. surfacemounttechnology (sMT) semakin digunakan dalam produk pembungkusan berketumpatan tinggi, seperti pakej tahap sistem (siP), peranti ballgridarray (BGA), dan Cip terdedah kuasa, pakej tanpa pin rata persegi (quad aatNo-lead, dirujuk sebagai QFN ) peranti.
Oleh kerana ciri-ciri proses dan bahan kimpalan tampal pateri, selepas kimpalan aliran semula peranti permukaan pateri yang besar ini, akan terdapat lubang di kawasan kimpalan pateri, yang akan menjejaskan sifat elektrik, sifat terma dan sifat mekanikal Prestasi produk, dan malah membawa kepada kegagalan produk, oleh itu, untuk memperbaiki rongga kimpalan aliran semula tampal pateri telah menjadi satu proses dan masalah teknikal yang mesti diselesaikan, beberapa penyelidik telah menganalisis dan mengkaji punca rongga kimpalan bola pateri BGA, dan menyediakan penyelesaian penambahbaikan, proses kimpalan aliran semula tampal pateri konvensional kawasan kimpalan QFN lebih besar daripada 10mm2 atau kawasan kimpalan lebih besar daripada penyelesaian cip kosong 6 mm2 kurang.
Gunakan kimpalan Preformsolder dan kimpalan relau refluks vakum untuk memperbaiki lubang kimpalan. Pateri pasang siap memerlukan peralatan khas untuk menunjuk fluks. Sebagai contoh, cip diimbangi dan dicondongkan dengan serius selepas cip diletakkan terus pada pateri pasang siap. Jika cip pelekap fluks adalah aliran semula dan kemudian titik, proses meningkat sebanyak dua aliran semula, dan kos bahan pateri pasang siap dan bahan fluks jauh lebih tinggi daripada pes pateri.
Peralatan refluks vakum lebih mahal, kapasiti vakum ruang vakum bebas adalah sangat rendah, prestasi kos tidak tinggi, dan masalah percikan timah adalah serius, yang merupakan faktor penting dalam penggunaan ketumpatan tinggi dan nada kecil. produk. Dalam makalah ini, berdasarkan proses kimpalan aliran semula tampal pateri konvensional, proses kimpalan aliran semula sekunder baru dibangunkan dan diperkenalkan untuk memperbaiki rongga kimpalan dan menyelesaikan masalah ikatan dan keretakan meterai plastik yang disebabkan oleh rongga kimpalan.
2 Rongga kimpalan dan mekanisme pengeluaran cetakan tampal pateri
2.1 Rongga kimpalan
Selepas kimpalan aliran semula, produk telah diuji di bawah x-ray. Lubang-lubang di zon kimpalan dengan warna yang lebih cerah didapati disebabkan oleh pateri yang tidak mencukupi dalam lapisan kimpalan, seperti ditunjukkan dalam Rajah 1
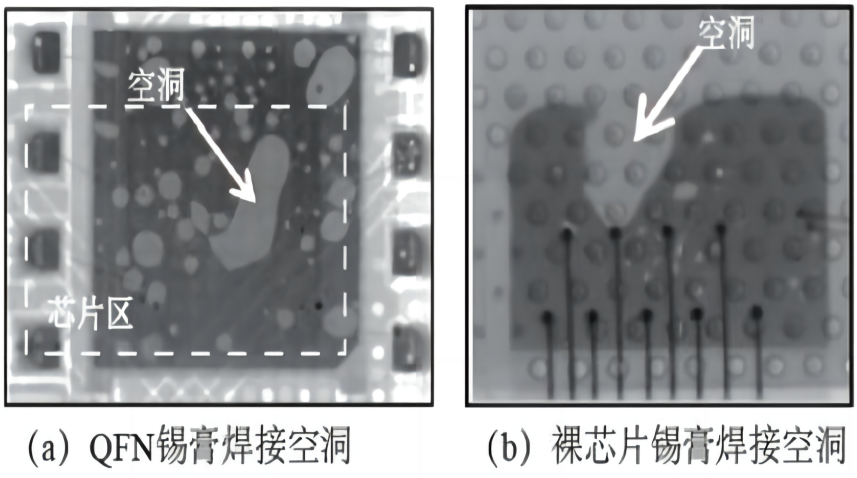
Pengesanan sinar-X bagi lubang gelembung
2.2 Mekanisme pembentukan rongga kimpalan
Mengambil pes pateri sAC305 sebagai contoh, komposisi dan fungsi utama ditunjukkan dalam Jadual 1. Fluks dan manik timah diikat bersama dalam bentuk tampal. Nisbah berat pateri timah kepada fluks adalah kira-kira 9:1, dan nisbah isipadu adalah kira-kira 1:1.
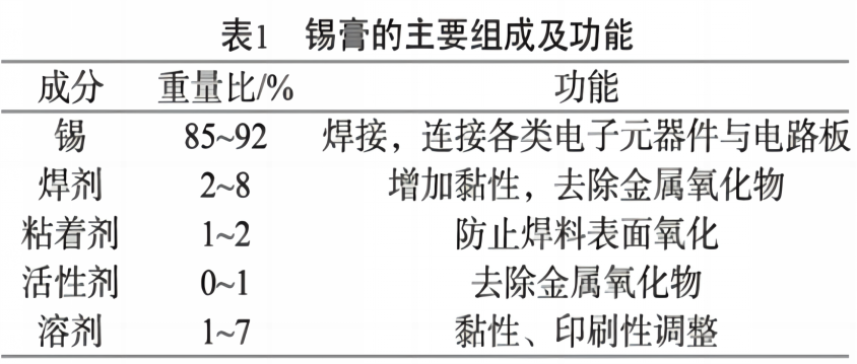
Selepas pes pateri dicetak dan dipasang dengan pelbagai komponen elektronik, pes pateri akan menjalani empat peringkat prapemanasan, pengaktifan, refluks dan penyejukan apabila ia melalui relau refluks. Keadaan pes pateri juga berbeza dengan suhu yang berbeza dalam peringkat yang berbeza, seperti yang ditunjukkan dalam Rajah 2.
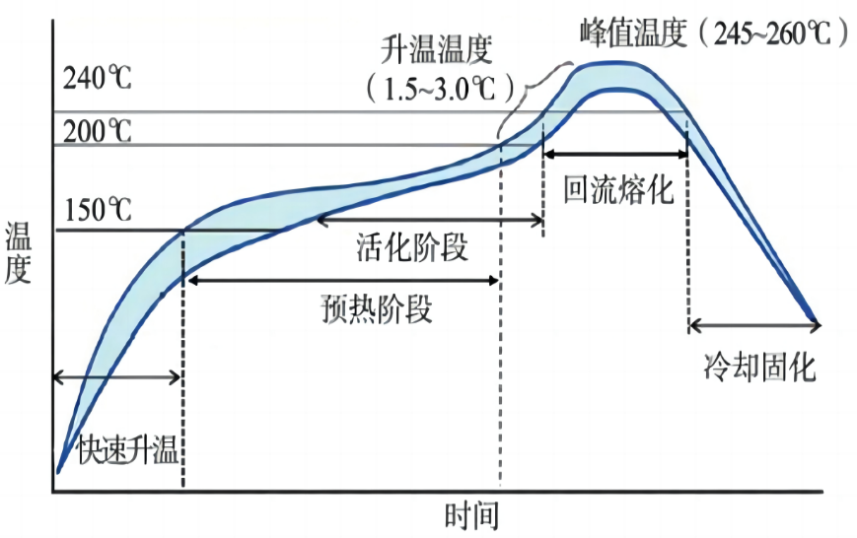
Rujukan profil untuk setiap kawasan pematerian aliran semula
Dalam peringkat prapemanasan dan pengaktifan, komponen meruap dalam fluks dalam pes pateri akan meruap menjadi gas apabila dipanaskan. Pada masa yang sama, gas akan terhasil apabila oksida pada permukaan lapisan kimpalan dikeluarkan. Sebahagian daripada gas ini akan meruap dan meninggalkan pes pateri, dan manik pateri akan terkondensasi rapat disebabkan oleh pemeruapan fluks. Pada peringkat refluks, fluks baki dalam pes pateri akan menguap dengan cepat, manik timah akan cair, sejumlah kecil gas meruap fluks dan sebahagian besar udara antara manik timah tidak akan tersebar dalam masa, dan baki dalam timah cair dan di bawah ketegangan timah cair adalah struktur sandwic hamburger dan ditangkap oleh pad pateri papan litar dan komponen elektronik, dan gas yang dibalut dalam tin cecair sukar untuk melarikan diri hanya dengan daya apungan ke atas Masa lebur atas adalah sangat singkat. Apabila timah cair menjadi sejuk dan menjadi timah pepejal, liang-liang kelihatan dalam lapisan kimpalan dan lubang pateri terbentuk, seperti yang ditunjukkan dalam Rajah 3.
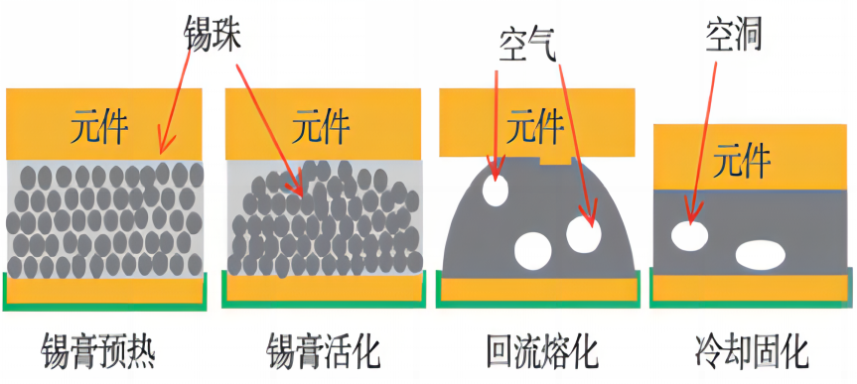
Gambarajah skematik lompang yang dihasilkan oleh kimpalan aliran semula tampal pateri
Penyebab utama rongga kimpalan ialah udara atau gas meruap yang dibalut dalam pes pateri selepas cair tidak dilepaskan sepenuhnya. Faktor-faktor yang mempengaruhi termasuk bahan tampal pateri, bentuk cetakan tampal pateri, jumlah cetakan tampal pateri, suhu refluks, masa refluks, saiz kimpalan, struktur dan sebagainya.
3. Pengesahan faktor-faktor yang mempengaruhi lubang kimpalan aliran semula cetakan tampal pateri
Ujian QFN dan cip kosong digunakan untuk mengesahkan punca utama lompang kimpalan aliran semula, dan untuk mencari cara untuk memperbaiki lompang kimpalan aliran semula yang dicetak oleh tampal pateri. Profil produk kimpalan aliran semula tampal pateri QFN dan cip kosong ditunjukkan dalam Rajah 4, saiz permukaan kimpalan QFN ialah 4.4mmx4.1mm, permukaan kimpalan adalah lapisan tin (100% timah tulen); Saiz kimpalan cip kosong ialah 3.0mmx2.3mm, lapisan kimpalan adalah lapisan dwilogam nikel-vanadium terpercik, dan lapisan permukaan adalah vanadium. Pad kimpalan substrat adalah celupan emas nikel-paladium tanpa elektro, dan ketebalannya ialah 0.4μm/0.06μm/0.04μm. Tampal pateri SAC305 digunakan, peralatan percetakan tampal pateri ialah DEK Horizon APix, peralatan relau refluks ialah BTUPyramax150N, dan peralatan x-ray ialah DAGExD7500VR.
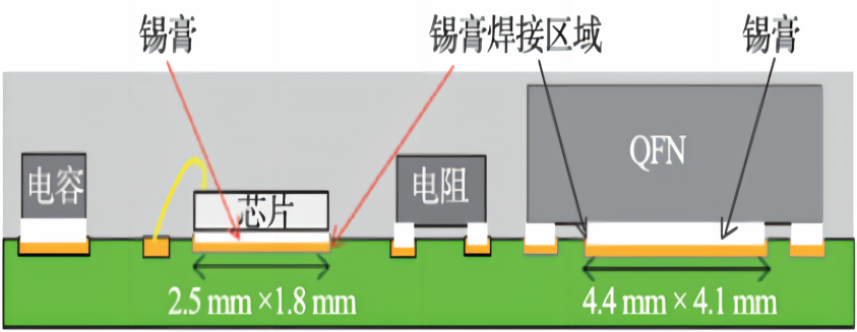
QFN dan lukisan kimpalan cip terdedah
Untuk memudahkan perbandingan keputusan ujian, kimpalan aliran semula dilakukan di bawah keadaan dalam Jadual 2.
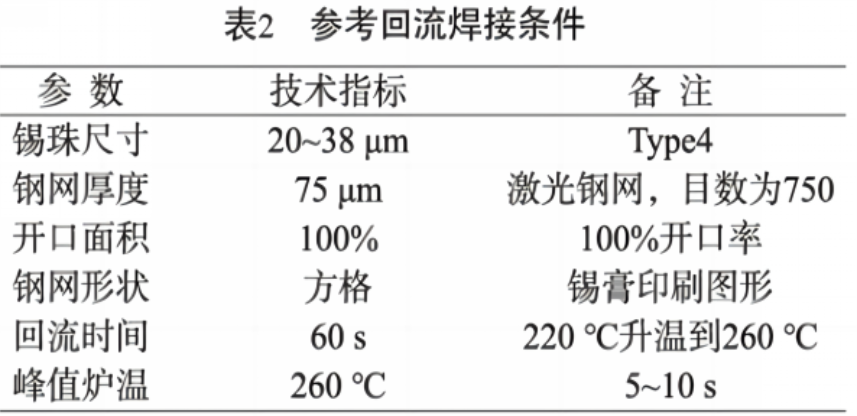
Jadual keadaan kimpalan aliran semula
Selepas pemasangan permukaan dan kimpalan aliran semula selesai, lapisan kimpalan telah dikesan oleh X-ray, dan didapati terdapat lubang besar pada lapisan kimpalan di bahagian bawah QFN dan cip kosong, seperti yang ditunjukkan dalam Rajah 5.
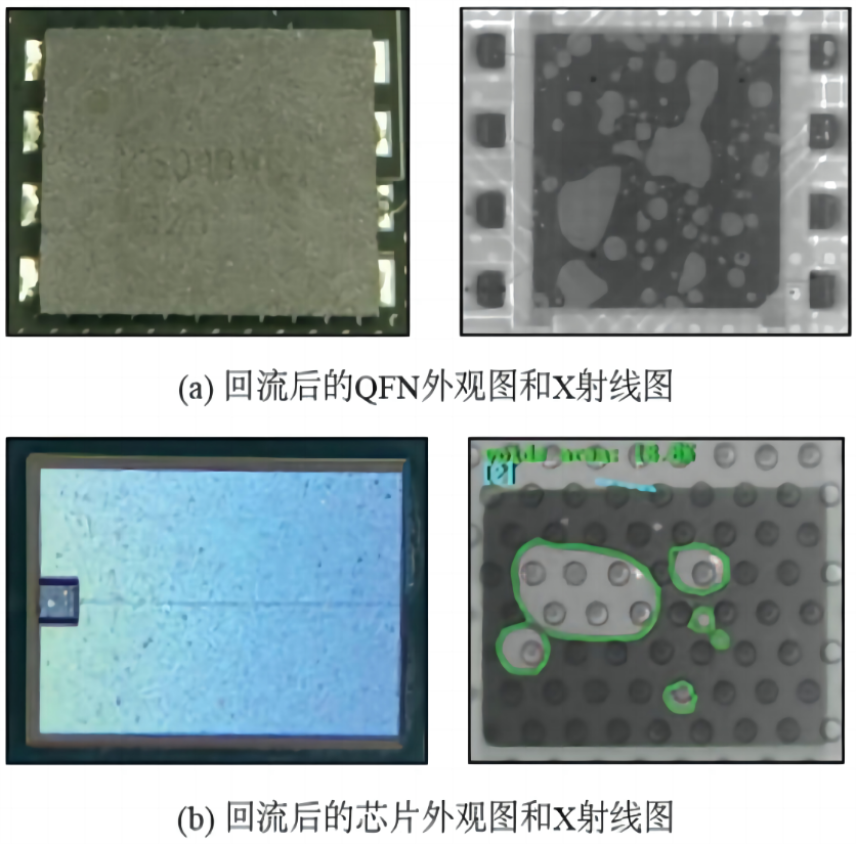
QFN dan Hologram Cip (X-ray)
Oleh kerana saiz manik timah, ketebalan jejaring keluli, kadar kawasan pembukaan, bentuk jejaring keluli, masa refluks dan suhu relau puncak semuanya akan menjejaskan lompang kimpalan aliran semula, terdapat banyak faktor yang mempengaruhi, yang akan disahkan secara langsung oleh ujian DOE, dan bilangan eksperimen. kumpulan akan menjadi terlalu besar. Adalah perlu untuk menyaring dan menentukan faktor-faktor yang mempengaruhi utama dengan cepat melalui ujian perbandingan korelasi, dan kemudian mengoptimumkan lagi faktor-faktor yang mempengaruhi utama melalui DOE.
3.1 Dimensi lubang pateri dan manik timah tampal pateri
Dengan ujian tampal pateri jenis3 (saiz manik 25-45 μm)SAC305, keadaan lain kekal tidak berubah. Selepas pengaliran semula, lubang dalam lapisan pateri diukur dan dibandingkan dengan tampal pateri jenis4. Didapati bahawa lubang pada lapisan pateri tidak berbeza dengan ketara antara kedua-dua jenis pes pateri, menunjukkan bahawa pes pateri dengan saiz manik yang berbeza tidak mempunyai pengaruh yang jelas pada lubang dalam lapisan pateri, yang bukan merupakan faktor yang mempengaruhi, seperti yang ditunjukkan dalam FIG. 6 Seperti yang ditunjukkan.
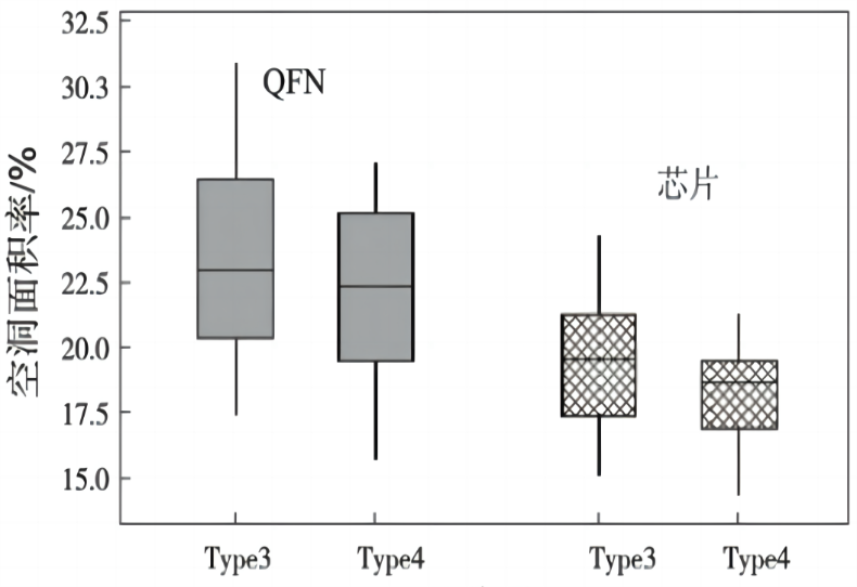
Perbandingan lubang serbuk timah logam dengan saiz zarah yang berbeza
3.2 Ketebalan rongga kimpalan dan jejaring keluli bercetak
Selepas pengaliran semula, kawasan rongga lapisan yang dikimpal diukur dengan mesh keluli bercetak dengan ketebalan 50 μm, 100 μm dan 125 μm, dan keadaan lain kekal tidak berubah. Didapati bahawa kesan ketebalan berbeza jaringan keluli (tampal pateri) pada QFN dibandingkan dengan jaringan keluli bercetak dengan ketebalan 75 μm Apabila ketebalan jaringan keluli bertambah, kawasan rongga beransur-ansur berkurangan. Selepas mencapai ketebalan tertentu (100μm), kawasan rongga akan terbalik dan mula meningkat dengan peningkatan ketebalan jejaring keluli, seperti yang ditunjukkan dalam Rajah 7.
Ini menunjukkan bahawa apabila jumlah pes pateri ditambah, tin cecair dengan refluks dilindungi oleh cip, dan alur keluar sisa udara keluar hanya sempit pada empat sisi. Apabila jumlah tampal pateri ditukar, salur keluar sisa udara keluar juga meningkat, dan letupan segera udara yang dibalut dengan timah cecair atau gas meruap yang keluar dari timah cecair akan menyebabkan timah cecair terpercik di sekitar QFN dan cip.
Ujian mendapati bahawa dengan peningkatan ketebalan jejaring keluli, gelembung pecah yang disebabkan oleh pelepasan udara atau gas meruap juga akan meningkat, dan kebarangkalian timah terpercik di sekitar QFN dan cip juga akan meningkat sejajar.
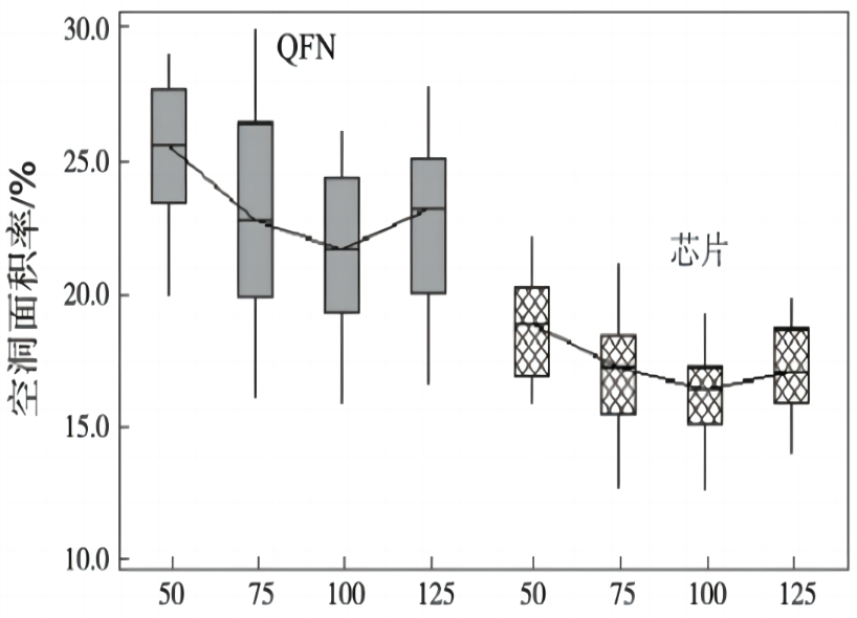
Perbandingan lubang dalam jejaring keluli dengan ketebalan yang berbeza
3.3 Nisbah kawasan rongga kimpalan dan bukaan jejaring keluli
Jaring keluli bercetak dengan kadar pembukaan 100%, 90% dan 80% telah diuji, dan keadaan lain kekal tidak berubah. Selepas pengaliran semula, kawasan rongga lapisan yang dikimpal diukur dan dibandingkan dengan jejaring keluli bercetak dengan kadar pembukaan 100%. Didapati tidak terdapat perbezaan yang ketara dalam rongga lapisan yang dikimpal di bawah keadaan kadar bukaan 100% dan 90% 80%, seperti yang ditunjukkan dalam Rajah 8.
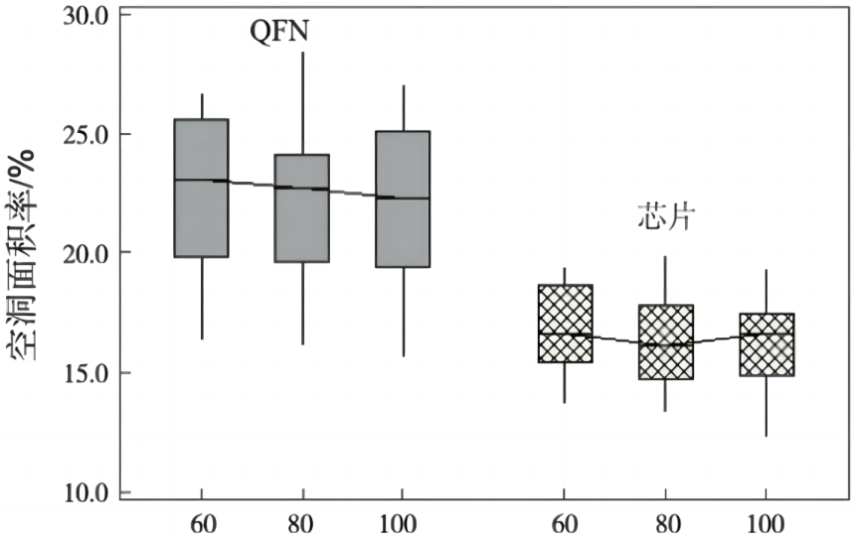
Perbandingan rongga kawasan bukaan yang berbeza bagi mesh keluli yang berbeza
3.4 Rongga dikimpal dan bentuk jejaring keluli bercetak
Dengan ujian bentuk cetakan pes pateri jalur b dan grid condong c, keadaan lain kekal tidak berubah. Selepas pengaliran semula, kawasan rongga lapisan kimpalan diukur dan dibandingkan dengan bentuk cetakan grid a. Didapati tiada perbezaan yang ketara dalam rongga lapisan kimpalan di bawah keadaan grid, jalur dan grid condong, seperti yang ditunjukkan dalam Rajah 9.
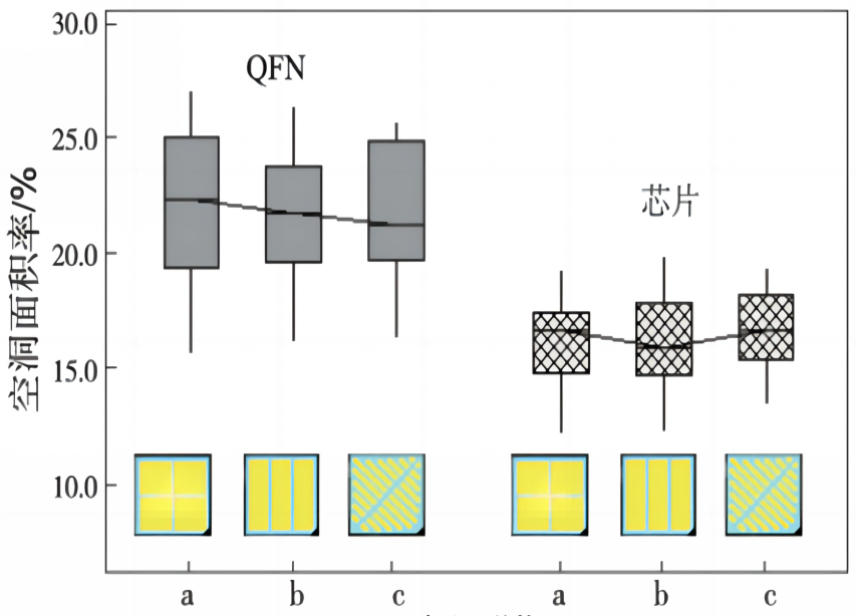
Perbandingan lubang dalam mod pembukaan yang berbeza bagi mesh keluli
3.5 Rongga kimpalan dan masa refluks
Selepas ujian masa refluks yang berpanjangan (70 s, 80 s, 90 s), keadaan lain kekal tidak berubah, lubang dalam lapisan kimpalan diukur selepas refluks, dan dibandingkan dengan masa refluks 60 s, didapati bahawa dengan peningkatan masa refluks, kawasan lubang kimpalan berkurangan, tetapi amplitud pengurangan secara beransur-ansur menurun dengan peningkatan masa, seperti yang ditunjukkan dalam Rajah 10. Ini menunjukkan bahawa dalam kes masa refluks yang tidak mencukupi, meningkatkan masa refluks adalah kondusif untuk limpahan penuh udara yang dibalut dengan timah cair cair, tetapi selepas masa refluks meningkat kepada masa tertentu, udara yang dibalut dalam tin cecair sukar untuk melimpah lagi. Masa refluks adalah salah satu faktor yang mempengaruhi rongga kimpalan.
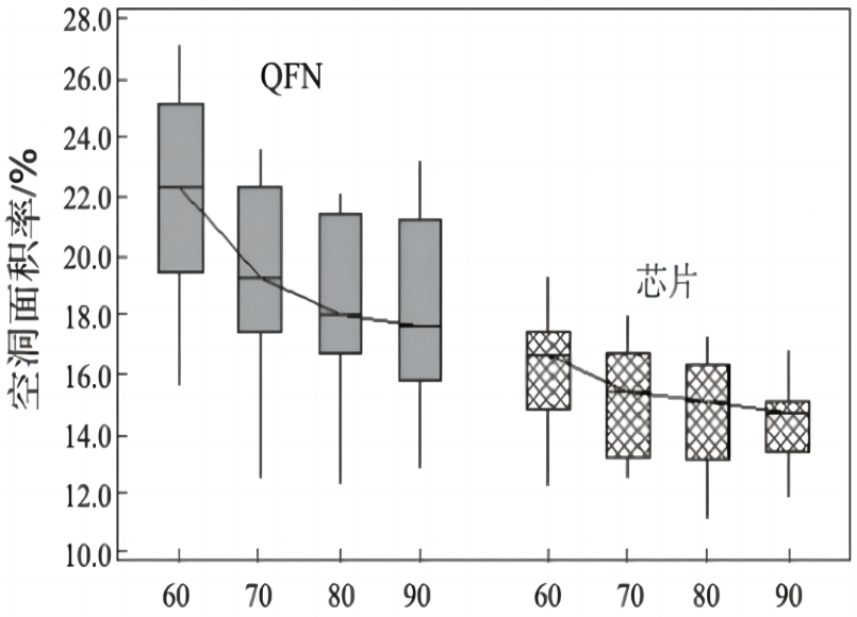
Perbandingan tidak sah bagi tempoh masa refluks yang berbeza
3.6 Rongga kimpalan dan suhu relau puncak
Dengan ujian suhu relau puncak 240 ℃ dan 250 ℃ dan keadaan lain yang tidak berubah, kawasan rongga lapisan yang dikimpal diukur selepas pengaliran semula, dan dibandingkan dengan suhu relau puncak 260 ℃, didapati bahawa di bawah keadaan suhu relau puncak yang berbeza, rongga lapisan QFN dan cip yang dikimpal tidak berubah dengan ketara, seperti yang ditunjukkan dalam Rajah 11. Ia menunjukkan bahawa puncak yang berbeza suhu relau tidak mempunyai kesan yang jelas pada QFN dan lubang pada lapisan kimpalan cip, yang bukan faktor yang mempengaruhi.
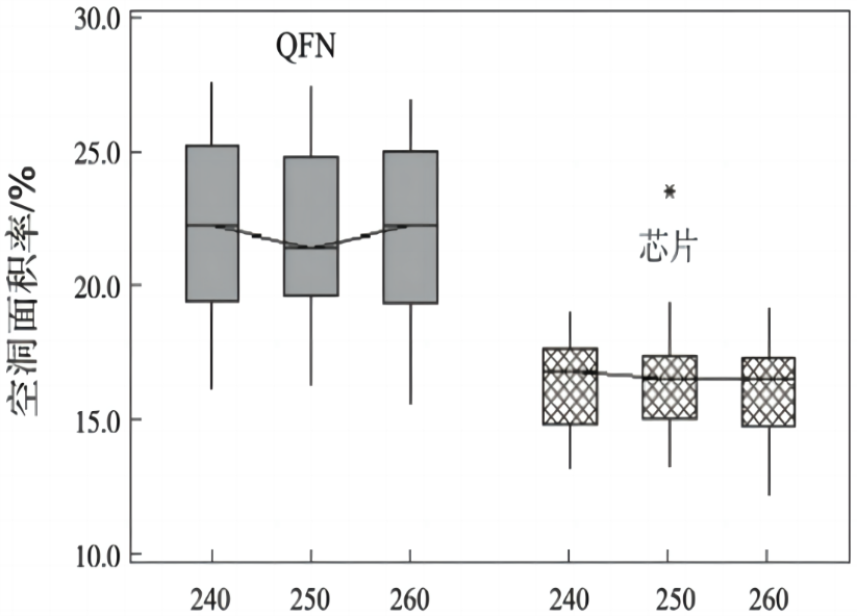
Perbandingan kosong bagi suhu puncak yang berbeza
Ujian di atas menunjukkan bahawa faktor penting yang mempengaruhi rongga lapisan kimpalan QFN dan cip ialah masa refluks dan ketebalan jaringan keluli.
4 Tampal pateri percetakan aliran semula pembaikan rongga kimpalan
4.1Ujian DOE untuk menambah baik rongga kimpalan
Lubang pada lapisan kimpalan QFN dan cip telah diperbaiki dengan mencari nilai optimum faktor pengaruh utama (masa refluks dan ketebalan jaringan keluli). Pes pateri ialah SAC305 type4, bentuk jejaring keluli adalah jenis grid (100% darjah pembukaan), suhu relau puncak ialah 260 ℃, dan keadaan ujian lain adalah sama seperti peralatan ujian. Ujian JAS dan keputusan ditunjukkan dalam Jadual 3. Pengaruh ketebalan jejaring keluli dan masa refluks pada QFN dan lubang kimpalan cip ditunjukkan dalam Rajah 12. Melalui analisis interaksi faktor-faktor yang mempengaruhi utama, didapati menggunakan ketebalan jejaring keluli 100 μm. dan masa refluks 80s boleh mengurangkan dengan ketara rongga kimpalan QFN dan cip. Kadar rongga kimpalan QFN dikurangkan daripada maksimum 27.8% kepada 16.1%, dan kadar rongga kimpalan cip dikurangkan daripada maksimum 20.5% kepada 14.5%.
Dalam ujian, 1000 produk telah dihasilkan di bawah keadaan optimum (100 μm ketebalan jejaring keluli, masa refluks 80 s), dan kadar rongga kimpalan 100 QFN dan cip diukur secara rawak. Purata kadar rongga kimpalan QFN ialah 16.4%, dan purata kadar rongga kimpalan cip ialah 14.7% Kadar rongga kimpalan cip dan cip jelas berkurangan.
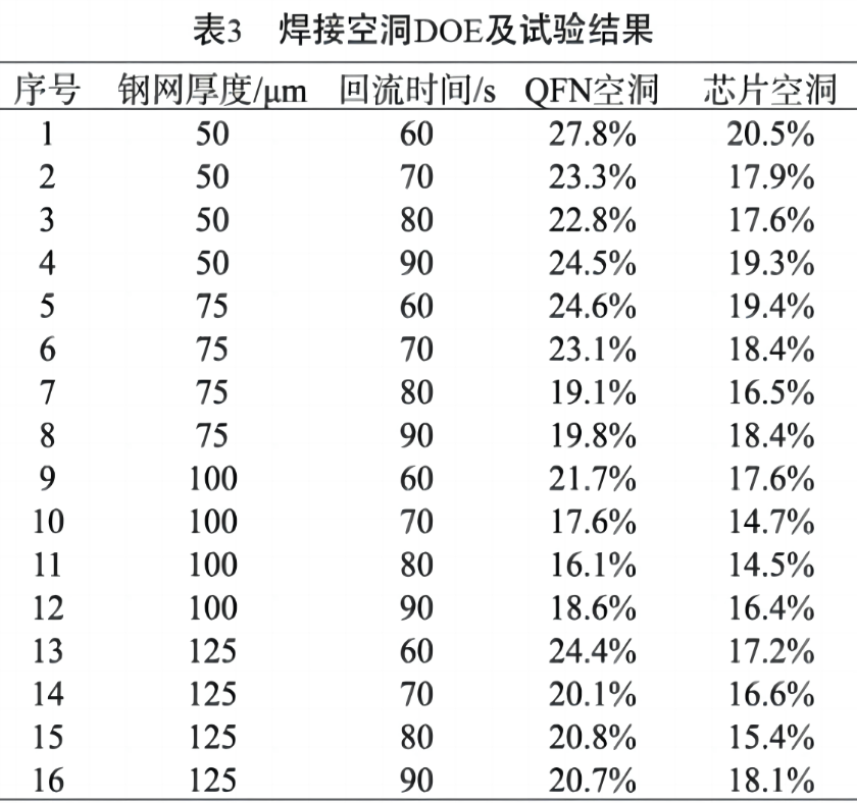
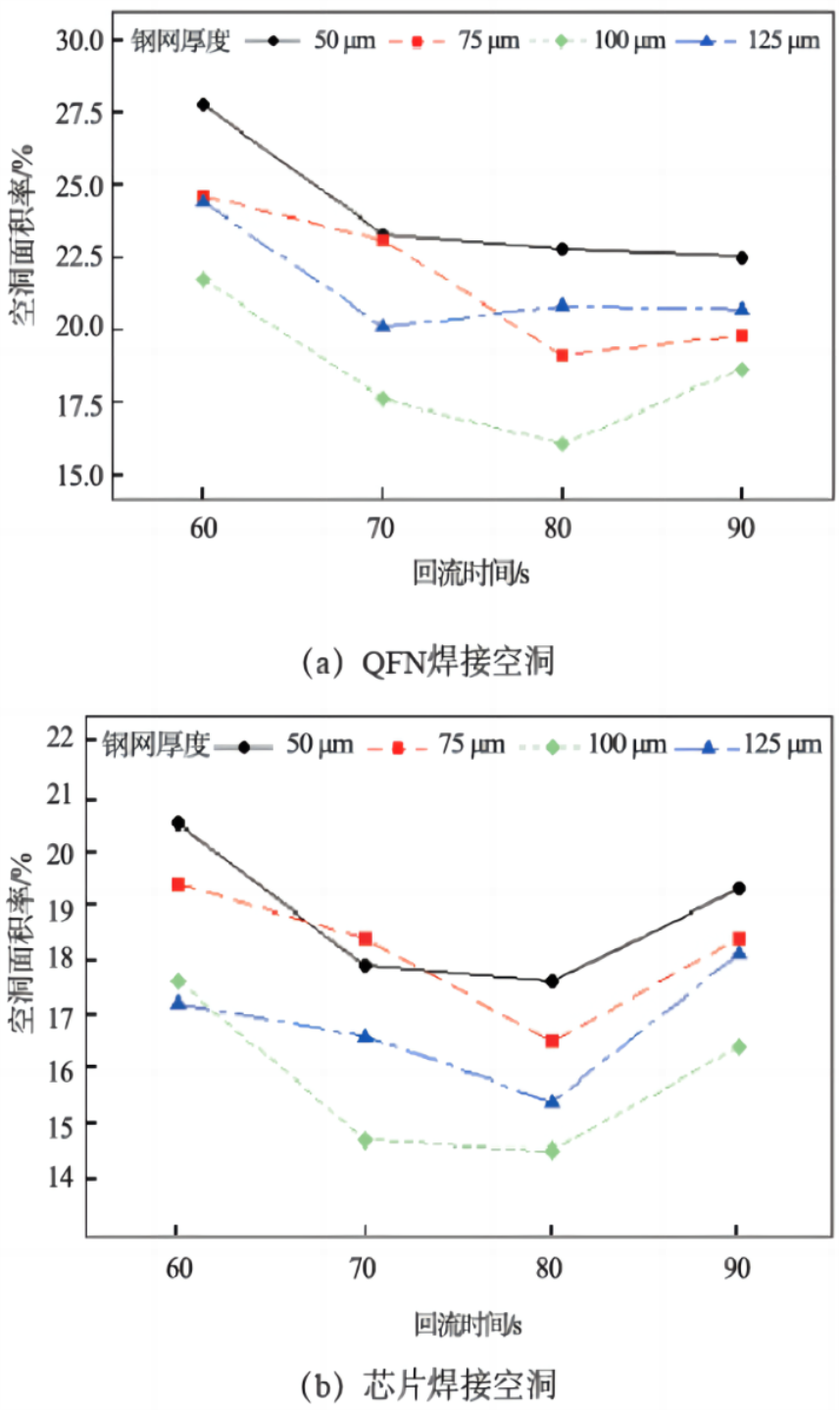
4.2 Proses baru menambah baik rongga kimpalan
Situasi pengeluaran dan ujian sebenar menunjukkan bahawa apabila kawasan rongga kimpalan di bahagian bawah cip adalah kurang daripada 10%, masalah keretakan kedudukan rongga cip tidak akan berlaku semasa ikatan dan pengacuan plumbum. Parameter proses yang dioptimumkan oleh JAS tidak dapat memenuhi keperluan untuk menganalisis dan menyelesaikan lubang dalam kimpalan aliran semula tampal pateri konvensional, dan kadar kawasan rongga kimpalan cip perlu dikurangkan lagi.
Oleh kerana cip yang dilindungi pada pateri menghalang gas dalam pateri daripada terlepas, kadar lubang di bahagian bawah cip dikurangkan lagi dengan menghapuskan atau mengurangkan gas bersalut pateri. Proses kimpalan aliran semula baharu dengan dua cetakan tampal pateri diguna pakai: satu cetakan tampal pateri, satu aliran semula tidak meliputi QFN dan cip kosong mengeluarkan gas dalam pateri; Proses khusus pencetakan tampal pateri sekunder, tampalan dan refluks sekunder ditunjukkan dalam Rajah 13.
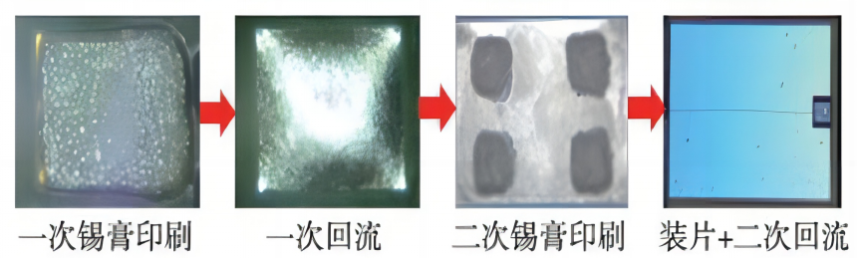
Apabila pes pateri tebal 75μm dicetak buat kali pertama, kebanyakan gas dalam pateri tanpa penutup cip terlepas dari permukaan, dan ketebalan selepas refluks adalah kira-kira 50μm. Selepas selesai refluks utama, petak kecil dicetak pada permukaan pateri pepejal yang disejukkan (untuk mengurangkan jumlah pes pateri, mengurangkan jumlah limpahan gas, mengurangkan atau menghapuskan percikan pateri), dan pes pateri dengan ketebalan 50 μm (keputusan ujian di atas menunjukkan bahawa 100 μm adalah yang terbaik, jadi ketebalan cetakan sekunder ialah 100 μm.50 μm=50 μm), kemudian pasang cip, dan kemudian kembali melalui 80 s. Hampir tiada lubang pada pateri selepas cetakan dan aliran semula pertama, dan tampal pateri dalam cetakan kedua adalah kecil, dan lubang kimpalan adalah kecil, seperti yang ditunjukkan dalam Rajah 14.
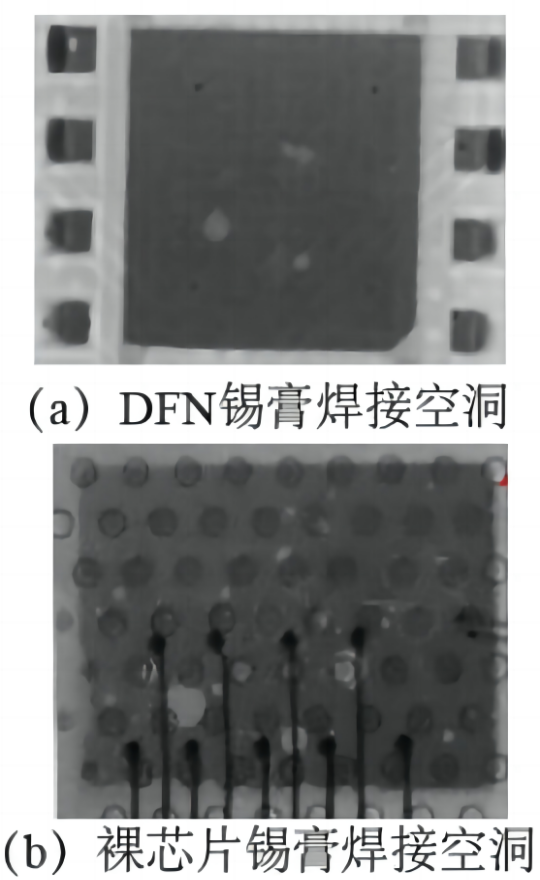
Selepas dua cetakan pes pateri, lukisan berongga
4.3 Pengesahan kesan rongga kimpalan
Pengeluaran 2000 produk (ketebalan mesh keluli percetakan pertama ialah 75 μm, ketebalan mesh keluli percetakan kedua ialah 50 μm), keadaan lain tidak berubah, pengukuran rawak 500 QFN dan kadar rongga kimpalan cip, mendapati bahawa proses baru selepas refluks pertama tiada rongga, selepas refluks kedua QFN Kadar rongga kimpalan maksimum ialah 4.8%, dan kimpalan maksimum kadar rongga cip ialah 4.1%. Berbanding dengan proses kimpalan pencetakan tampal tunggal asal dan proses pengoptimuman JAS, rongga kimpalan berkurangan dengan ketara, seperti yang ditunjukkan dalam Rajah 15. Tiada retak cip ditemui selepas ujian kefungsian semua produk.
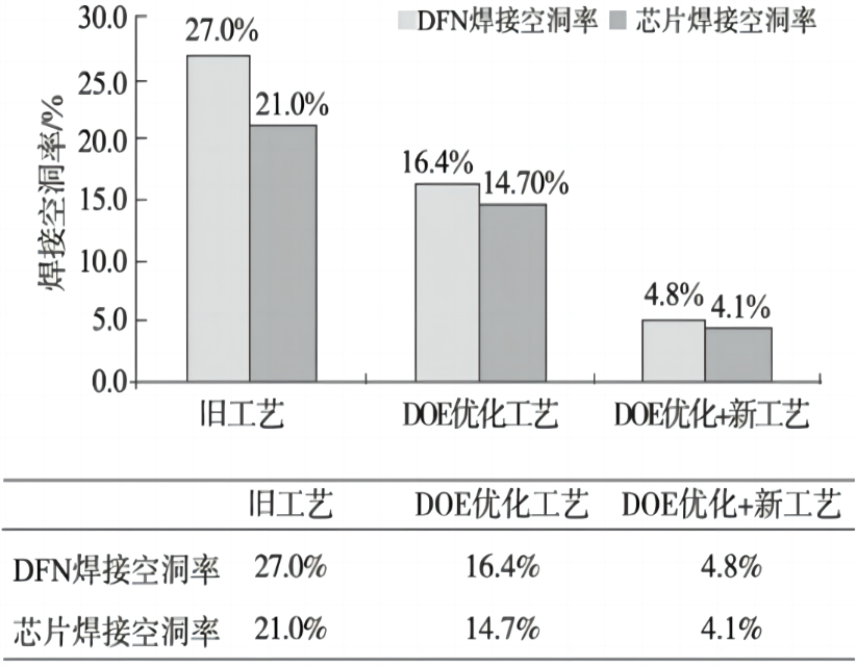
5 Ringkasan
Pengoptimuman jumlah cetakan pes pateri dan masa refluks boleh mengurangkan kawasan rongga kimpalan, tetapi kadar rongga kimpalan masih besar. Menggunakan dua teknik kimpalan aliran semula cetakan tampal pateri boleh berkesan dan memaksimumkan kadar rongga kimpalan. Kawasan kimpalan cip kosong litar QFN boleh menjadi 4.4mm x4.1mm dan 3.0mm x2.3mm masing-masing dalam pengeluaran besar-besaran Kadar rongga kimpalan aliran semula dikawal di bawah 5%, yang meningkatkan kualiti dan kebolehpercayaan kimpalan aliran semula. Penyelidikan dalam kertas kerja ini memberikan rujukan penting untuk memperbaiki masalah rongga kimpalan permukaan kimpalan kawasan yang besar.
Masa siaran: Jul-05-2023